下面重點介紹幾種常用的表面工程技術。
2.1 熱噴涂
熱噴涂法不僅能使零件具有耐磨、耐蝕、耐氧化、耐高溫、隔熱等不同功能,而且能使它具有復合性能,即能保護零件,又能修復零件。目前,在發動機中,主要用于曲軸、活塞頂部、活塞環、氣缸套、排氣門、閥座、凸輪、齒輪等零件的表面處理和修復,表1給出了采用熱噴涂修復發動機缸體及更換新件的經濟效益對比,由表可見,熱噴涂3Cr13材料修復僅需花費新件成本的4.2%。
表1 熱噴涂3Cr13經濟效益分析
在發動機中,用于提高零件表面耐磨性的噴涂材料主要有下列幾種:
1)鉬。鉬作為噴涂材料,其純度需在99.95%以上。鉬主要作為活塞環的噴層,它可以得到具有氧化物層的層狀鉬層和大約10%~15%的孔隙率,其噴涂層厚度一般為0.25mm,具有良好的儲油性能。鉬層熔點高(約為2620℃)、摩擦系數低、硬度高(HV1070左右)。因此耐磨性好,一般用在第一道活塞環處。
2)鉬基合金。鉬基合金的等離子噴涂層的特點是抗拉缸性好,因為它是由低硬度的純鉬(HV350)和硬度相當高的(HV700)鎳基合金兩相組成。其熱穩定性優于鉬絲噴涂層,耐磨性能相當于鍍鉻,特別是在潤滑條件不夠充分時。
3)鉻基合金。鉻基合金等離子噴涂層不僅在邊界條件下的耐磨性及抗咬和性能較好,而且還能提高配磨材料的耐磨性,可同時提高缸套和活塞環的耐磨性[11]。在邊界潤滑條件下,這種涂層的活塞環比鍍鉻還更耐磨,因此,可做高速、中速和低速發動機活塞環的涂層材料。
4)陶瓷。陶瓷涂層如氧化鉻和氧化鋁/二氧化鈦硬度較高(HV1500),在一定條件下,活塞環的耐磨性能好,但對缸套磨損卻很大,因此,只能在特殊要求的情況下使用。
5)金屬陶瓷。金屬陶瓷是比較復雜的,它是以碳化物為基(如碳化鎢)的涂層,即使在惡劣的運轉條件下,不但活塞環的磨損低,缸套的磨損也低。但金屬陶瓷很貴。在發動機中,一般將陶瓷噴在排氣閥面、活塞頂面、活塞環工作面上。
6)鎳基合金。鎳基合金有Ni-B-Si和Ni-Cr-B-Si系。鎳基合金涂層除耐磨性較好外,還有很好的抗蝕性和較高的熱硬性。主要用于發動機活塞環、閥座、閥門、凸輪的噴焊(也用于修復),以提高這些零件的耐磨性。
7)高碳鋼與不銹鋼。高碳鋼,如碳素工具鋼T8常用于修復并強化發動機鑄鋼,球墨鑄鐵軸頸表面的線材氣噴、電噴涂。而不銹鋼由于具有優越的耐蝕性、耐熱性,而用于氣缸套內表面的噴涂(火焰噴),具有很好的效果。
2.2 電刷鍍修復
發動機凸輪軸軸頸的主要失效方式是磨損或劃傷,以前凸輪軸軸頸出現磨損或劃傷一般就報廢了,或者采用加厚軸瓦的辦法磨削軸頸后使用,給用戶的維修帶來很大的麻煩。電刷鍍技術具有設備簡單、操作方便、安全可靠、鍍積速度快的特點,用于修復凸輪軸軸頸取得明顯效果。表2給出了采用電刷鍍納米Al2O3/Ni修復發動機輪軸和連桿的效益分析,電刷鍍技術可大大降低維修成本。
表2 電刷鍍n-Al2O3/Ni經濟效益分析

2.3 擠滲碳化硅
擠滲碳化硅工藝是把碳化硅微粒直接擠滲到金屬表面層,在其表面呈非連續分布。這種方法的主要特點是工藝簡單、生產效率高、成本低廉、無污染、無須特殊設備。因此,它是一種很有前途的新工藝。主要用于提高發動機氣缸套、活塞環的耐磨性,特別對高強載發動機更有效。
2.4 鍍鉻
鍍鉻工藝主要用于提高發動機零件的耐磨損與耐腐蝕性,如曲軸軸頸,十字頭軸頸,活塞銷、活塞環槽,活塞桿、缸套、活塞環、氣閥及閥桿鍍鉻、油泵柱塞和套筒。目前,發動機零部件中常用的耐磨鍍鉻有兩種,硬質鍍鉻和松孔鍍鉻。
硬質鍍鉻是指硬度較高而又耐磨的光亮鍍鉻層,它主要用于潤滑條件較好,負荷又不很大的條件下,一般鍍層厚度為0.03~0.3mm,最厚可達到1.0mm。
松孔鍍鉻主要用于潤滑不良,承受載荷較大的零件如發動機缸套、活塞環、十字頭銷等。
2.5 氮化
氮化有三種:(1)普通氮化,指純粹氮原子的滲入;(2)軟氮化,鹽浴液體軟氮化,含有活性氮、碳原子的氣體介質中的氣體軟氮化及離子軟氮化(包括加鈦離子氮化);(3)輝光離子氮化。
目前,最常用和最有發展前途的是離子軟氮化和輝光離子氮化。它們主要用來提高發動機零件如曲軸軸頸、缸套、活塞環、凸輪軸、進排氣閥、氣門挺桿等的耐磨性、耐疲勞和耐腐蝕等。
2.6 激光加熱表面淬火
激光加熱用于鋼和鑄鐵零件表面淬火,以提高其耐磨性。美國GM645系列柴油機,為了解決缸套氣口的拉傷和提高其耐磨性,對氣口部位曾分別進行過氮化、感應加熱淬火和火焰淬火等處理,但由于處理面很大、溫度高,出現了嚴重變形,甚至發生裂紋,最后用激光加熱表面淬火處理,取得了良好的效果[12]。激光加熱淬火的氣缸活塞環在我國已有應用,而且反映良好。該方法的特點是工藝簡單、變形很小(如對缸套表面淬火,局部溫度可達916℃,其它部位溫度低于200℃,因此變形很小)。
2.7 噴丸加工
噴丸加工法不需改變零部件的形狀、材料、熱處理,而且易于提高強度,特別是疲勞強度,因此,在發動機中已有很多應用,目前主要應用于曲軸、連桿、氣閥彈簧、搖臂及傳動齒輪等部位。經噴丸加工后的強化層可達0.5~0.6mm,表面硬度可達HRC40~50左右。
2.8 冷壓光加工
作為光整和表面強化的手段,冷壓光加工在生產中得到了日益廣泛的應用,以改善其零件表層的質量(粗糙度、冷硬程度、冷硬層深度、殘余應力的性質和大小)。在發動機中主要用于氣缸套、活塞銷孔、連桿小頭銅襯套、氣閥導管、閥桿表面、凸輪軸頸、曲軸軸頸,特別是曲柄臂過渡圓的最后精加工,用以降低表面粗糙度及其強化并呈現殘余壓應力。
3 結 論
綜上所述,由于發動機零部件的工作條件復雜,損壞常常是幾種失效形式的復合,對零部件表面性能的要求往往不是單一的。因此,只有根據零部件的工況條件和失效特點正確選用表面強化方法,才能達到延長零部件的使用壽命和節約材料的目的。
(中國工程機械動力部件網)
[來源:百度文庫,如有知識產權爭議,請聯系微信X37329588]。
獲得更多最新產品知識庫知識及行業資訊,請掃描微信二維碼,關注微信,關注中國工程機械動力部件網!
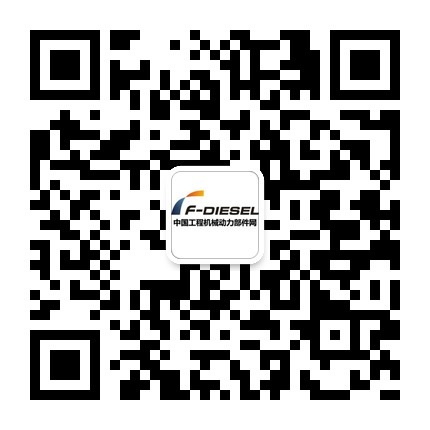